- Beiträge: 376
- Dank erhalten: 9
- Forum
- Drivers - Pub
- Markenunabhängige Themen
- Pickup Aufbauten, Wohnkabinen und Wohnwagen
- Bird´s Baubericht - Expeditionskabine Ford Ranger
Bird´s Baubericht - Expeditionskabine Ford Ranger
- Bird
-
Autor
- Offline
- Platinum Boarder
-
Weniger
Mehr
31 Dez 2013 20:25 - 31 Dez 2013 20:38 #1
von Bird
Wir sind ein freies Land:
Hier kann jeder MEINE Meinung haben
Bird´s Baubericht - Expeditionskabine Ford Ranger wurde erstellt von Bird
Hallo zusammen,
schon lange versprochen gibt es hier nun den ersten Teil vom Baubericht einer kleinen voll geländetauglichen Mini-Wohnkabine für meinen Ford Ranger (BJ 2004.
Der Umbau stellt nun wohl den (vorläufig?)
letzte Umbau meines guten alten Rangers dar. Der Umbau spiegelt die Evolution vom „PU Rohling als Kleinlaster“ hin zum Reisefahrzeug. Dabei sind die Erfahrungen aus unseren Urlauben mit Dachzelt auf einer Alpentour, so manchen Besuchen in Offroad Fahrgeländen, den Erfahrungen von guten Bekannten und mehreren Touren auf Island, eingeflossen.
Vor dem Umbau:
Und der aktuelle Zwischenstand:
Geschlossenes Dach:
Mit aufgestelltem Dach:
Mehr Bilder vom ersten Test auf Island hier: Klick
Da ich, trotz mittlerweile doch recht großem Angebot an Kabinen, nicht wirklich etwas passendes gefunden habe (und für eine Sonderanfertigung leider nicht den passenden Lottogewinn verfüge
) blieb nur ein kompletter Eigenentwurf von der ersten Bleistift- und CAD Zeichnung bis über den Bau vom Zwischenrahmen und der Kabine selber.
Vorab: Da ich mit der Kabine keinen Schönheitspreis gewinnen wollte und der ganze Bau überwiegend draußen unter freiem Himmel erfolgen musste und obendrein Zeit bei mir leider immer Hexenwerk ist, ging Funktionalität vor Schönheit
Die in das Design eingeflossenen wichtigsten Grundüberlegungen:
- Die Kabine sollte so robust sein, dass sie einen Rempler im Gelände und die Belastung durch Gelände, Wellblechpiste und rauen Umgang möglichst Unbeschadet überlebt. (Fenster bei geschlossenem Deckel geschützt)
- Max Gewicht des Fahrzeug gegenüber Dachzeltlösung nicht erhöhen. Unterfahrschutz, größerer 130l Tank + 20 l Reserve, zwei Batterien 75 Ah, zwei Seilwinden, Windenstoßstange, Schwellerschutz, Standheizung und und und sammeln sich ohnehin schon.
(Daher keine Absetzkabine und feste Kabine aus CFK/Kevlar auf einem Sandwich-Paneel)
- Abmessungen des Fahrzeuges so bemessen, dass ein (Not-) Transport im Container weiterhin möglich ist. Zum einen sollte das Fahrzeug doch mal defekt zurück transportiert werden müssen, oder für das ein oder andere entfernte Urlaubsziel. Grundsätzlich: je kleiner, desto besser im Gelände, auch sollte der Schwerpunkt so niedrig wie möglich gehalten werden aus Erfahrung so mancher Piste. (Wer schon mal ein Schneefeld wieder herabgerutscht ist, weiß wie wenig der Tip nie den Wagen quer zum Hang zu bringen wirklich umsetzbar ist, wenn der „Kleine“ einfach der Schwerkraft folgt...
)
- Klappdach mit festen überlappende Wände und keinem Zeltstoff (Primäres Urlaubsziel Island mit potentiell Sturm, Hagel, Regen aber auch mal Wintercamping) und um den Windwiderstand und den Schwerpunkt bei der Fahrt möglichst niedrig zu halten!
- Möglichkeit das ohne Betten- Umbau eine Person schlafen und min 1 Person sitzen kann.
- Möglichkeit das Fahrzeug auch weiterhin nebenbei als "rollende Werkzeugbox", zum Bauschutttransport, Gartenabfalltransporter, Baumarktgroßeinkauf, Holzholen im Wald, Umzug und was-weiß-ich-noch Universalpickuptransporter nutzen zu können. Fußbodenbereich daher so, dass er mit Schlamm und Schutt zurecht kommt und anstelle von festen Schränken zum Teil Standard- Werkzeugboxen, die es in verschiedenen Größen gibt.
- Einbruchsmöglichkeiten so weit wie möglich reduzieren, daher alle Fenster bei geschlossenem Deckel verdeckt und auch die Einstiegstür wird dadurch doppelt gesichert.
- Genügend auch von Außen zugänglicher Stauraum. Damit ergab sich auch auch der Bereich hinter der Faherkabine, der modular entweder für eine Alubox + zweites Reserverad und Erdanker, oder zweites Reserverad + 4 x 20 l Reservekanister + Erdanker oder weiteren Varianten je nach Einsatz genutzt werden kann. Gerade für Zusatzdiesel, Kettensägensprit, Sägen, dreckigen Bergegurten und dem Müllbeutel wollte ich einen Stauraum außerhalb der Kabine haben, ähnlich dem guten alten originalen Pickup.
- Keine eigenen Nasszelle, da wir bisher immer auch so Duschmöglichkeiten hatten. Platz für Porta Potti bei Bedarf vorhanden, meißt nutzen wir „Toi Toi Felsen“ ;o) (Ein paar sehr nette Schweizer, die wir inzwischen auf Island getroffen haben meinten, durch den „Wannenaufbau“ der Kabine könnte man ruhig auch drinnen eine Dusche verbauen, ein Abfluß im Fußboden wäre eh kein Problem – Also Option für Später)
- Durchreiche zur Fahrerkabine, damit durch die Fahrzuglüftung bei Fahrt auch eine Durchlüftung der Kabine stattfindet und sich selbst bei schlechtem Wetter auf Dauer kein Kondenswasser sammelt.
- Eigentlich war auch gedacht eine Europalette mit den Abmessungen 120 x 80 cm weiterhin transportieren zu können. Allerdings mangels gefundener Tür mit 85cm Innenbreite und zu Gunsten eines größeres Außenstauraums bei gleicher Fahrzeuglänge dann entfallen. Würde ich bei einem erneuten Bau jedoch wohl berücksichtigen.
So begann erst alles mit vielen Bleistiftplanungen aber erst mal genug Text und ein paar Bilder:
Der Umbau begann mit dem Entfernen der Ladefläche um die Befestigungspunkte genau zu vermessen und um für die Winde und zweite Batterie eine neue Trägerkonstruktion zu bauen. Nebenbei sollte auch die AH Kupplung zu Gunsten des hinteren Böschungswinkels entfallen. Benötige die eh nur zum Bergen, und dafür sind zwei Aufnahmen für Schäkel eingeplant.
Dabei wurden auch gleich 10kg Sand und Schlamm aus dem Rahmen entfernt... Wenn ich bedenke, dass man auf Island für 30g Vulkanasche etwa 10 Euro im Souvenirshop zahlt... Ich bin reich! ;o)
Nun ging es daran eine neue Halterung für die hintere 5,5t Seilwinde und eine neue Stoßstange zu bauen. Ebenso wie die neue Halterung für die Rückleuchten. Hier bin ich auf Rückleuchten vom MAN TGA umgestiegen, finde ich ganz passend und sind ohne Probleme beim TÜV dank E- Prüfzeichen.
Das Untergestell entsteht aus 4-Kant Material. Die Bereiche an denen das Gestell mit dem Rahmen verschraubt wird, sind mit 3mm satrkem Blech verstärkt. Hatte lange Zeit trotz rechnerischem OK doch die Befürchtung, das die Wandstärken doch zu gering sind, aber Toi Toi Toi.. alles auch nach ausgiebigem Test auf Island alles ok. Die Verwindungen des Fahrzeug Rahmens werden über Dämpfer aus 4mm PUR aufgenommen.
Der 40l Wassertank findet seinen Platz aus Frostgründen innerhalb der Kabine.
Die Windenkonsole mit den zwei Schäkel Aufnahmen als Abschleppösen und der Ausziehleiter mit Nummernschildhalter. Die Teleskopleiter ist aus dem Bootszubehör und aus rostfreiem Stahl.
Als nächstes wurde ein neuer Halter für die zweite hintere Batterie gebaut. Dieser ist später nur durch ein Alublech im Bereich für das zweite Reserverad verschlossen und somit endlich von oben zugänglich. Gut zu sehen ist auch der Long Ranger Tank, das Old Man EMU Fahrwerk und der Druckluftanschluss der ARB Differentialsperre, so wie die höher gelegte Differentialentlüftung.
Weiter ging es mit dem Bau der Halterungen für einen 20L Reservekanister, einen 10L Wasserkanister und je Seite einer Alubox. Alles so tief wie möglich um den Schwerpunkt unten zu halten und so dicht wie möglich an der Achse um die Kräfte gering zu halten.
Der Halter für das Reserverad wurde auch etwas nach vorne Versetzt um den hinteren Böschungswinkel zu vergrößern und den Abstand zur Heckleiter sicherzustellen.
So sieht das dann die Anordnung final aus. Die Kabel für die Winde und Rücklichter finden auch ihren Platz.
Das Grundgestell nimmt Form und Farbe, na ja zumindest Grundierung an.
Der Boden und die Seitenflächen werden isoliert und alle Hohlräume ausgeschäumt bevor die ersten Lagen Kohlefasergewebe von unten und oben zur Wasserdichtigkeit laminiert werden.
Die Heckscheibe ist entfernt um den Durchbruch zur Fahrerkabine zu ermöglichen. (Auf dem Bild verschlossen durch das Alublech) Als Beschichtung habe ich mich für ein PU Coating entschieden.
Rechts unten ist die höhergelegte Tankentlüftung zu sehen. Als Abschluss dient ein „Sprudelstein“ aus dem Aquariumzubehör. Dieser lässt genügend Luft durch, Schmutzpartikel kommen jedoch nicht ohne weiteres durch. Im Vordergrund ist auch die Alu Abdeckplatte zu sehen unter der die Batterie und später auch die Standheizung zugänglich ist. Dieser Bereich ist dann der von außen zugängliche Stauraum für das zweite Reserverad, Erdanker und Ähnliches.
Damit war der erste Teil des Umbaus grob abgeschlossen. Nun ging es weiter in 3D um die genauen Abmessungen für das Sandwich Material und das Zwischengestell zu bekommen...
Abmessungen des Fahrzeugs mit Stoßstange bis Hinterkante Aufbau sind nun 5,5m Länge, 1,83m Breite und ca. 2,44m Höhe. Mit Aufgeklapptem Dach innen 1,9m Stehhöhe.
Auf der Suche nach einem passenden Sandwichpaneel bin ich auf der Abenteuer Allrad in Bad Kissingen über den Stand der Firma Paneeltec GmbH gestoßen und habe dort erfahren, dass es auch möglich wäre ein Sandwich Paneel ohne Gelcoat Deckschicht mit nur jeweils ca. 1,2 mm GFK Trägerschicht zu bekommen, was für mein Vorhaben nahezu perfekt ist. (Nachträglich sollte ja darauf mit CFK Laminiert werden).
Nach einigen E-Mails mit echt erstklassiger technischer Beratung durch die Firma Paneeltec GmbH war ich als stolzer Besitzer von 29,8 m² Paneel mit 25 mm Stärke, 18 x 600ml Schläuchem mit „Körapop 225 als Kleber + Reiniger und Haftvermittler.
Für mich ein besonderes Plus die Platten mit einer Grüße von bis zu 2,1m x 3m wurden persönlich angeliefert. Immerhin über eine Entfernung von ca 500km!
Ich glaube Herr M. hatte dabei allerdings auch seinen Spaß, denn der Gesichtsausdruck, als er sah das ich alles nur in der Garage verarbeiten wollte, sah für mich aus wie... ohh je – So viel schönes Sandwich und so wenig Chance, dass daraus jemals eine Kabine wird …
Aber davon mehr im nächsten Teil.
Mit besten Grüßen und einen guten Rutsch!
Bird
schon lange versprochen gibt es hier nun den ersten Teil vom Baubericht einer kleinen voll geländetauglichen Mini-Wohnkabine für meinen Ford Ranger (BJ 2004.
Der Umbau stellt nun wohl den (vorläufig?)

Vor dem Umbau:
Und der aktuelle Zwischenstand:
Geschlossenes Dach:
Mit aufgestelltem Dach:
Mehr Bilder vom ersten Test auf Island hier: Klick

Da ich, trotz mittlerweile doch recht großem Angebot an Kabinen, nicht wirklich etwas passendes gefunden habe (und für eine Sonderanfertigung leider nicht den passenden Lottogewinn verfüge

Vorab: Da ich mit der Kabine keinen Schönheitspreis gewinnen wollte und der ganze Bau überwiegend draußen unter freiem Himmel erfolgen musste und obendrein Zeit bei mir leider immer Hexenwerk ist, ging Funktionalität vor Schönheit

Die in das Design eingeflossenen wichtigsten Grundüberlegungen:
- Die Kabine sollte so robust sein, dass sie einen Rempler im Gelände und die Belastung durch Gelände, Wellblechpiste und rauen Umgang möglichst Unbeschadet überlebt. (Fenster bei geschlossenem Deckel geschützt)
- Max Gewicht des Fahrzeug gegenüber Dachzeltlösung nicht erhöhen. Unterfahrschutz, größerer 130l Tank + 20 l Reserve, zwei Batterien 75 Ah, zwei Seilwinden, Windenstoßstange, Schwellerschutz, Standheizung und und und sammeln sich ohnehin schon.
(Daher keine Absetzkabine und feste Kabine aus CFK/Kevlar auf einem Sandwich-Paneel)
- Abmessungen des Fahrzeuges so bemessen, dass ein (Not-) Transport im Container weiterhin möglich ist. Zum einen sollte das Fahrzeug doch mal defekt zurück transportiert werden müssen, oder für das ein oder andere entfernte Urlaubsziel. Grundsätzlich: je kleiner, desto besser im Gelände, auch sollte der Schwerpunkt so niedrig wie möglich gehalten werden aus Erfahrung so mancher Piste. (Wer schon mal ein Schneefeld wieder herabgerutscht ist, weiß wie wenig der Tip nie den Wagen quer zum Hang zu bringen wirklich umsetzbar ist, wenn der „Kleine“ einfach der Schwerkraft folgt...

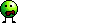
- Klappdach mit festen überlappende Wände und keinem Zeltstoff (Primäres Urlaubsziel Island mit potentiell Sturm, Hagel, Regen aber auch mal Wintercamping) und um den Windwiderstand und den Schwerpunkt bei der Fahrt möglichst niedrig zu halten!
- Möglichkeit das ohne Betten- Umbau eine Person schlafen und min 1 Person sitzen kann.

- Möglichkeit das Fahrzeug auch weiterhin nebenbei als "rollende Werkzeugbox", zum Bauschutttransport, Gartenabfalltransporter, Baumarktgroßeinkauf, Holzholen im Wald, Umzug und was-weiß-ich-noch Universalpickuptransporter nutzen zu können. Fußbodenbereich daher so, dass er mit Schlamm und Schutt zurecht kommt und anstelle von festen Schränken zum Teil Standard- Werkzeugboxen, die es in verschiedenen Größen gibt.
- Einbruchsmöglichkeiten so weit wie möglich reduzieren, daher alle Fenster bei geschlossenem Deckel verdeckt und auch die Einstiegstür wird dadurch doppelt gesichert.
- Genügend auch von Außen zugänglicher Stauraum. Damit ergab sich auch auch der Bereich hinter der Faherkabine, der modular entweder für eine Alubox + zweites Reserverad und Erdanker, oder zweites Reserverad + 4 x 20 l Reservekanister + Erdanker oder weiteren Varianten je nach Einsatz genutzt werden kann. Gerade für Zusatzdiesel, Kettensägensprit, Sägen, dreckigen Bergegurten und dem Müllbeutel wollte ich einen Stauraum außerhalb der Kabine haben, ähnlich dem guten alten originalen Pickup.
- Keine eigenen Nasszelle, da wir bisher immer auch so Duschmöglichkeiten hatten. Platz für Porta Potti bei Bedarf vorhanden, meißt nutzen wir „Toi Toi Felsen“ ;o) (Ein paar sehr nette Schweizer, die wir inzwischen auf Island getroffen haben meinten, durch den „Wannenaufbau“ der Kabine könnte man ruhig auch drinnen eine Dusche verbauen, ein Abfluß im Fußboden wäre eh kein Problem – Also Option für Später)
- Durchreiche zur Fahrerkabine, damit durch die Fahrzuglüftung bei Fahrt auch eine Durchlüftung der Kabine stattfindet und sich selbst bei schlechtem Wetter auf Dauer kein Kondenswasser sammelt.
- Eigentlich war auch gedacht eine Europalette mit den Abmessungen 120 x 80 cm weiterhin transportieren zu können. Allerdings mangels gefundener Tür mit 85cm Innenbreite und zu Gunsten eines größeres Außenstauraums bei gleicher Fahrzeuglänge dann entfallen. Würde ich bei einem erneuten Bau jedoch wohl berücksichtigen.

So begann erst alles mit vielen Bleistiftplanungen aber erst mal genug Text und ein paar Bilder:
Der Umbau begann mit dem Entfernen der Ladefläche um die Befestigungspunkte genau zu vermessen und um für die Winde und zweite Batterie eine neue Trägerkonstruktion zu bauen. Nebenbei sollte auch die AH Kupplung zu Gunsten des hinteren Böschungswinkels entfallen. Benötige die eh nur zum Bergen, und dafür sind zwei Aufnahmen für Schäkel eingeplant.
Dabei wurden auch gleich 10kg Sand und Schlamm aus dem Rahmen entfernt... Wenn ich bedenke, dass man auf Island für 30g Vulkanasche etwa 10 Euro im Souvenirshop zahlt... Ich bin reich! ;o)

Nun ging es daran eine neue Halterung für die hintere 5,5t Seilwinde und eine neue Stoßstange zu bauen. Ebenso wie die neue Halterung für die Rückleuchten. Hier bin ich auf Rückleuchten vom MAN TGA umgestiegen, finde ich ganz passend und sind ohne Probleme beim TÜV dank E- Prüfzeichen.
Das Untergestell entsteht aus 4-Kant Material. Die Bereiche an denen das Gestell mit dem Rahmen verschraubt wird, sind mit 3mm satrkem Blech verstärkt. Hatte lange Zeit trotz rechnerischem OK doch die Befürchtung, das die Wandstärken doch zu gering sind, aber Toi Toi Toi.. alles auch nach ausgiebigem Test auf Island alles ok. Die Verwindungen des Fahrzeug Rahmens werden über Dämpfer aus 4mm PUR aufgenommen.
Der 40l Wassertank findet seinen Platz aus Frostgründen innerhalb der Kabine.
Die Windenkonsole mit den zwei Schäkel Aufnahmen als Abschleppösen und der Ausziehleiter mit Nummernschildhalter. Die Teleskopleiter ist aus dem Bootszubehör und aus rostfreiem Stahl.
Als nächstes wurde ein neuer Halter für die zweite hintere Batterie gebaut. Dieser ist später nur durch ein Alublech im Bereich für das zweite Reserverad verschlossen und somit endlich von oben zugänglich. Gut zu sehen ist auch der Long Ranger Tank, das Old Man EMU Fahrwerk und der Druckluftanschluss der ARB Differentialsperre, so wie die höher gelegte Differentialentlüftung.
Weiter ging es mit dem Bau der Halterungen für einen 20L Reservekanister, einen 10L Wasserkanister und je Seite einer Alubox. Alles so tief wie möglich um den Schwerpunkt unten zu halten und so dicht wie möglich an der Achse um die Kräfte gering zu halten.
Der Halter für das Reserverad wurde auch etwas nach vorne Versetzt um den hinteren Böschungswinkel zu vergrößern und den Abstand zur Heckleiter sicherzustellen.
So sieht das dann die Anordnung final aus. Die Kabel für die Winde und Rücklichter finden auch ihren Platz.
Das Grundgestell nimmt Form und Farbe, na ja zumindest Grundierung an.

Der Boden und die Seitenflächen werden isoliert und alle Hohlräume ausgeschäumt bevor die ersten Lagen Kohlefasergewebe von unten und oben zur Wasserdichtigkeit laminiert werden.
Die Heckscheibe ist entfernt um den Durchbruch zur Fahrerkabine zu ermöglichen. (Auf dem Bild verschlossen durch das Alublech) Als Beschichtung habe ich mich für ein PU Coating entschieden.
Rechts unten ist die höhergelegte Tankentlüftung zu sehen. Als Abschluss dient ein „Sprudelstein“ aus dem Aquariumzubehör. Dieser lässt genügend Luft durch, Schmutzpartikel kommen jedoch nicht ohne weiteres durch. Im Vordergrund ist auch die Alu Abdeckplatte zu sehen unter der die Batterie und später auch die Standheizung zugänglich ist. Dieser Bereich ist dann der von außen zugängliche Stauraum für das zweite Reserverad, Erdanker und Ähnliches.
Damit war der erste Teil des Umbaus grob abgeschlossen. Nun ging es weiter in 3D um die genauen Abmessungen für das Sandwich Material und das Zwischengestell zu bekommen...
Abmessungen des Fahrzeugs mit Stoßstange bis Hinterkante Aufbau sind nun 5,5m Länge, 1,83m Breite und ca. 2,44m Höhe. Mit Aufgeklapptem Dach innen 1,9m Stehhöhe.
Auf der Suche nach einem passenden Sandwichpaneel bin ich auf der Abenteuer Allrad in Bad Kissingen über den Stand der Firma Paneeltec GmbH gestoßen und habe dort erfahren, dass es auch möglich wäre ein Sandwich Paneel ohne Gelcoat Deckschicht mit nur jeweils ca. 1,2 mm GFK Trägerschicht zu bekommen, was für mein Vorhaben nahezu perfekt ist. (Nachträglich sollte ja darauf mit CFK Laminiert werden).
Nach einigen E-Mails mit echt erstklassiger technischer Beratung durch die Firma Paneeltec GmbH war ich als stolzer Besitzer von 29,8 m² Paneel mit 25 mm Stärke, 18 x 600ml Schläuchem mit „Körapop 225 als Kleber + Reiniger und Haftvermittler.
Für mich ein besonderes Plus die Platten mit einer Grüße von bis zu 2,1m x 3m wurden persönlich angeliefert. Immerhin über eine Entfernung von ca 500km!
Ich glaube Herr M. hatte dabei allerdings auch seinen Spaß, denn der Gesichtsausdruck, als er sah das ich alles nur in der Garage verarbeiten wollte, sah für mich aus wie... ohh je – So viel schönes Sandwich und so wenig Chance, dass daraus jemals eine Kabine wird …

Aber davon mehr im nächsten Teil.
Mit besten Grüßen und einen guten Rutsch!
Bird
Wir sind ein freies Land:
Hier kann jeder MEINE Meinung haben

Letzte Änderung: 31 Dez 2013 20:38 von Bird.
Bitte Anmelden oder Registrieren um der Konversation beizutreten.
- Ingo
-
- Offline
- Administrator
-
01 Jan 2014 13:23 #2
von Ingo
...gesendet von meinem Desktop PC mit Röhrenmonitor....
Ingo antwortete auf Bird´s Baubericht - Expeditionskabine Ford Ranger
Frohes Neues!
Geil, das ist doch mal ein toller Bericht! Danke fürs erstellen!
Da hast Du dir aber viel Arbeit gemacht, was sich aber gelohnt hat. Sieht wirklich super gut und praktisch aus.
Bin schon auf den nächsten Teil gespannt!
Gruß Ingo
Geil, das ist doch mal ein toller Bericht! Danke fürs erstellen!
Da hast Du dir aber viel Arbeit gemacht, was sich aber gelohnt hat. Sieht wirklich super gut und praktisch aus.
Bin schon auf den nächsten Teil gespannt!
Gruß Ingo
...gesendet von meinem Desktop PC mit Röhrenmonitor....
Bitte Anmelden oder Registrieren um der Konversation beizutreten.
- BigPit
-
- Offline
- Moderator
-
01 Jan 2014 13:35 #3
von BigPit
BigPit antwortete auf Bird´s Baubericht - Expeditionskabine Ford Ranger
Saubere, bewundernswere Arbeit.
Alle Achtung! wohl dem, der schweißen kann und den Platz für ein solches Projekt hat. Ich bin auf die Fortsetzungen gespannt.
Alle Achtung! wohl dem, der schweißen kann und den Platz für ein solches Projekt hat. Ich bin auf die Fortsetzungen gespannt.
Bitte Anmelden oder Registrieren um der Konversation beizutreten.
- Bird
-
Autor
- Offline
- Platinum Boarder
-
Weniger
Mehr
- Beiträge: 376
- Dank erhalten: 9
01 Jan 2014 17:15 - 01 Jan 2014 17:17 #4
von Bird
Wir sind ein freies Land:
Hier kann jeder MEINE Meinung haben
Bird antwortete auf Bird´s Baubericht - Expeditionskabine Ford Ranger
Hallo zusammen,
vielen Dank schon mal für das Feedback.
So eine lange Sylvesternacht und ein freier Tag ist gar nicht so verkehrt, daher schon heute und nicht erst wieder in einem Jahr der Teil 2 des Bauberichtes.

Da ich von Anfang an vorhatte, auf das Sandwich-Paneel eine (oder je nach Belastung mehrere) Lagen aus CFK und aus Gründen der höheren Schlagzähigkeit eine Decklage Aramid (Kevlar)/CFK Hybridgewebe aufzubringen, war ich nicht an den Einsatz von sonst üblichen Eckprofilen an den Stößen der Sandwichpaneele gebunden.
Damit war ich in der Formgebung der Kabine praktisch völlig frei und die Kabine hat wesentlich mehr Abschrägungen, als „Normale“ Kabinen bekommen.
Ja ja - 3D CAD Software verleitet immer zum spielen... Nur gut, dass der Entwurf nicht durch eine Arbeitsvorbereitung ging, die hätten mich wieder gelyncht
Ich wollt jedoch den Windwiderstand so gering wie möglich halten und die Kabine sollte auch nicht ganz so wuchtig auf dem kleinen Pickup wirken.... und ja zugegeben, man(n) möchte sich ja auch immer etwas von der Masse absetzen
Daraus ergab sich dann natürlich eine recht große Anzahl an Puzzleteilen die alle ohne Verschnitt passend gesägt werden mussten…
Für alle die ähnliches vorhaben, ich rate dazu für die Schnitte unbedingt eine Führungsschiene für Kreissägen zu besorgen. Ich hatte mir zwei mal 1,4m und noch eine 0,8m Schiene besorgt + die zugehörigen Verbinder. So konnte ich auch die längsten Schnitte mit über 3m in einem Stück sauber an der Schiene sägen.
Da ich alles nur in der kleinen Garage gemacht habe, hatte ich damit auch gleich das Problem gewonnen, wie die übereinander liegenden Paneele sägen, ohne das Untere gleich mit anzusägen...
Gelöst habe ich das Problem recht simpel mit 3cm starken Styroporplatten die ich jeweils immer über die komplette Fläche unter das oberste Paneel geschoben habe. So habe ich nur ca 5mm in das Styropor gesägt.
Was ich bei der Arbeit auch lieben gelernt habe ist eine Akku Kreissäge. Kein Kabelgezuppel, das sich garantiert irgendwo verhakt und ewig stört... Was unbedingt nicht sparen sollte ist eine gute und gute sitzende Staubmaske! Einige Schnitte habe ich gleich auch mit Absaugung durchgeführt, aber der Schlauch stört zugegeben doch auch wieder
Ohne Werbung machen zu wollen, aber von Makita gibt es seid ner Weile kleine 10,8V Maschinen. Unter anderem eine kleine Akku-Kreissäge und Akku-Stichsäge. Ein Traum für alle die Kleinteile und Öffnungen für Stauraumklappen. Die Arbeit soll ja auch Spaß bringen.
Wo wir gerade beim Thema Spaß sind... Auch wenn sich der ganze Umbau nun schon über einen ewigen Zeitraum hinstreckt, war der eigentliche Bau der Kabine dann doch eher Stress und weniger Spaß als erhofft.... Beruflich bedingt viel mehrfach der geplante Urlaub zum Bau aus, und die Zeit bis zum schon lange mit dem TÜV vereinbarten Termin für die Abnahme wurde eng... Letztendlich blieben dann genau 9 Tage um vom ersten Puzzle Teil ein vom TÜV abnahmefähiges Fahrzeug herzustellen
Also hieß es „Meter machen“ und gerade beim Laminieren ist so manch nicht so schöne Ecke dem Zeitdruck oder der Müdigkeit geschuldet... Die letzten Tage fingen Morgens gegen ca 8:30 an und endeten um 4 Uhr in der Früh... zusammen mit den Ausdünstungen von Harz und Aceton ist dann einem vieles egal
Aber zurück zum Bau. Nachdem die Puzzeleteile soweit ausgesägt waren habe ich den unteren Teil der Kabine über Kopf aufgebaut und erst einmal mit Tape zusammengefügt um noch eine letzte Pass-Kontrolle vorzunehmen und alles auszurichten. Ein paar große Zwingen ein Haufen kleinerer und Spanngurte sollten dabei unbedingt vorhanden sein.
Das von der Firma Paneeltec vorgeschlagene Körapop 225 ließ sich sehr gut verarbeiten und hatte eine hervorragende Klebeleistung. Vor allem ließ es sich auch mit dem passenden Lösungsmittel (noch nicht getrocknet) gut von der Oberfläche entfernen.
Ein Teil der Paneele wurden als Sitzfläche und Staubox gleich in die Kabine integriert. Dies führt gleichzeitig zu mehr Verwendungsstabilität bei gleichzeitig geringem Gewicht.
Die Längs und Querwände sind so angeordnet, das die Kräfte vom Fahrzeugrahmen optimal in die Kabine eingetragen werden und praktisch jede Wand vom Aufbau tragend ist, was die Kräfte gut verteilt.
Danach ging es an das erste Laminieren.
Die Firma „HP-Textiles“ konnte sich über diverse Aufträge freuen. Darunter:
- 65m² CFK/Aramid Hybridgewebe 205g/m2 Körper
- 25m² Kohlefasergewebe 420g/m2 Körper
- 20m² Kohlefasergewebe 245g/m² Körper
- 75m x 4cm Carbonband UniDirektional ca. 340g/m²
- Epoxi-System HP-E55L (Harz + Härter) Laminierharzsystem
- Epoxi-System HP-E40D (Harz + Härter) Deckschichtharzsystem
- Verdünner XB 5 Liter
- Abreissgewebe
- Viele Restbestände über "321...Meins"
Da die Liegefläche mit 210cm praktisch auf der Beifahrerseite über die komplette Länge „frei schwebt“ müssen hier die nur recht kurzen Wände die kompletten Biege-/ Zugkräfte aufnehmen. Auch der Boden muss dementsprechend stabil sein. Daher wurde hier erst mit 450g Gewebe gearbeitet und als Decklage das Hybridgewebe. In den Kanten wurde jeweils eine zweite Lage 450g/m² Gewebe verarbeitet um die Kräfte abzuleiten.
Die spätere Auflage für das Klappdach wurde in Form einer halbrund Holzleiste mit eingearbeitet.
Das Hybridgewebe mit Körperbindung ließ sich sehr gut drapieren und ließ sich somit auch sehr gut um die Kannten legen. Da sich das Hybridgewebe durch sein Kevlar kaum/praktisch nicht mit einer normalen Schere schneiden lässt, hatte ich mir neben einer Mikroverzahnten Schere einen „Easy Cutter“ Klick ich bin ein Link mit Mikroverzahnung gekauft. Auch wenn das gute Teil doch den Eindruck von viel „Plaste“ hinterlässt, doch absolut Top für diesen Einsatz!
Nachdem die Außenseite soweit fertig war, durfte der(die) Heizlüfter zeigen wofür unsere „grüner“ Strom so taugt und die Garage auf 40° zum Tempern für eine Nacht und einen halben Tag hochheizen.
Mehr war zeitlich leider nicht drin... Das Klappdach rief und so musste erst mal das Unterteil raus und gedreht werden. Obwohl eigentlich zu erwarten waren wir doch vom geringen Gewicht überrascht. Da ist das Dachzelt um Längen schwerer...

Problemlos ließ sich das Unterteil zu Zweit raustragen und auch drehen, ohne das es auseinanderbrach. So den ein oder anderen kritischen Blick der Nachbarschaft gab es dabei schon...
Nun wurde das ganze wieder „richtig herum“ in die Garage verfrachtet und der Deckel angepasst. Die große Herausforderung bestand nun darin, das durch den unteren offenen Querschnitt doch recht instabile Gebilde so auf Dauer zu bändigen, dass auch nach dem Zusammenbau der Spalt die gleiche Breite behält...sonst ist essig mit Abdichten...
Das war eigentlich auch meine größte Sorge beim Entschluss eine geteilte Kabine zu bauen und hat mich zwischenzeitlich zig mal wieder in die Richtung gezogen doch eine „Einteilige“ zu bauen. Letztendlich sorgt die spätere Dichtung auch noch für eine zusätzliche Spreizkraft .
Und als ob das ganze nicht schon schwer genug wäre, wollte ich den Deckel auch noch so stabil haben, dass ich auch noch drauf stehen kann oder etwas drauf verzurren kann. Das im geschlossenen Zustand nur ca. 4cm von der Seitenwand des Deckels über der des Unterteils stehen (rote Pfeile), macht die Sache nicht unbedingt einfacher... Also doch mal gut das man(n) Schiffbau studiert hat und aus Siebdruckplatte zwei Spanten (grüner Pfeil) ausgesägt und mit etwas Vorspannung eingeklebt und (bis das ganze laminiert ist) provisorisch verschraubt.
Kaum das der Kleber etwas Zeit hatte zu trocknen, kam der Deckel auch schon runter um in tiefer Nacht das Unterteil aus der Garage zu holen um die Hochzeit des Unterteils mit dem Untergestell zu starten. „Petrina“ (Ein Mann könnte beim Wetter noch so launisch sein) zeigte Einsicht und ließ am nächsten Tag die Sonne scheinen.
Um das Sandwich mit dem Metallgestell zu verkleben habe ich Sikaflex 260 verwendet. (Das im Gegensatz zum Körapop später wirklich überall seine Spuren hinterläst und man hat auch Wochenlang schöne schwarze Pfoten...) Über die Klebekraft lässt sich aber nicht meckern.
Tja nun ließ sich zum ersten Mal grob erkennen wie es später als Fahrzeug aussehen würde... Kurze Pause – Zum ersten Mal seid Tagen ein Teechen in Ruhe... Und weiter, Tag ist kurz...
Flugs das gute Wetter genutzt um den Liegebereich zu laminieren. (Ein Königreich für eine Halle)
Daher wurde hier wieder erst mit 450g Gewebe gearbeitet und in den Seitenwänden kam in Hauptbelastungsrichtung und als Kantenabschluss ein Unidirektionales Gelege zur Anwendung um die Zugkräfte aufzunehmen.
Schon jetzt konnte ich alleine durch die Außenlagen immerhin bis zur Vorderkannte robben um dort zu laminieren, ohne das die Liegefläche abbrach.
Sieg!
Auf dem Bild ist auch gut der Durchbruch zur Fahrerkabine zu sehen. Ich war schon erleichtert, als beide Ausschnitte tatsächlich deckungsgleich waren.
Schnell Abplanen und dann ging es die Nacht weiter daran den Deckel zu laminieren. Bis heute ärgert mich dabei eine Beule auf der Rückseite des Deckels, die man immer schön sieht von Hinten. Allerdings unter der Berücksichtigung, dass ich zu dem Zeitpunkt so gegen 03:30 bereits +18h Arbeit an dem Tag hinter mir und in den Knochen hatte wundert mich das es nur eine ist, die ich übersehen habe.

Den nächsten Tag durfte der Deckel auch bei ca 40° vor sich „hintempern“, während ich draußen den Übergang zwischen Unterteil und Metallgestell laminiert habe und die Auflageleiste, auf der der Deckel später im geschlossen Zustand liegen sollte. Schnell auch noch alle Übergänge geschliffen und die eine Stauraumklappe eingebaut. Der TÜV Termin rückte näher...
Am nächsten Tag dann der große Moment. Würde der Deckel auch nach dem Laminieren auf das Unterteil passen??? Zusammen mit unserem Nachbarn der sich netter Weise sofort zur Unterstützung angeboten hat, haben wir den Deckel aufgesetzt.
Und sitzt...in der Länge etwas knapp, aber passt!
Nun musste noch das Scharnier zum Klappen eingebaut werden. Dafür hatte ich mir überlegt einfach einen Bolzen zu verwenden. Woher Bolzen und Lager nehmen und nicht stehlen? Not macht erfinderisch, ich hatte noch von meinen alten Blattfedern die Bolzen aus den Federschäkeln und noch die Polyurethanlagerbuchsen. Also erst 8mm durchgebohrt und dann mit einer 32mm Lochsäge nachgebohrt. Lagerbuchsen mit angedicktem 5 min Epoxy eingesetzt und den Bolzen eingesetzt. Andere Seite ebenfalls und eine Stunde später der entscheidende Moment: Drehpunkt richtig gewählt, lässt sich der Deckel nun öffnen?
Er lies... Pühhhhh
Also schnell noch die Dachluke eingesetzt (Notwendig als zweiter Fluchtweg). Hatte mir dafür über „321..meins“ eine Bootsluke gekauft, die die geforderten 500x 500mm Innendurchmesser hat und neben abschließbar auch noch eine Stellung mit „Lüften“ hat, sprich sich mit nur wenigen mm Öffnung verriegeln lässt.
Am nächsten Morgen dann der Moment der Wahrheit: es ging zum TÜV. Die Hecktür war zwar noch nicht eingebaut und die Fenster lagen nur im Fahrzeug, aber... Details...
Ca. 1 ½ Stunden bangen und ich war stolzer Besitzer einer neuen Eintragung: „Teleskopierbarer Expeditionskoffer mit seitlichen Halterungen für Staukästen“ Doppelpühhhh alles soweit vom TÜV abgenommen.
Ich bin auf eigenen Wunsch weiterhin LKW geblieben (So hat mein Kleiner das Licht des Montagehalle erblickt und so soll er auch bleiben) allerdings nur noch mit zwei Sitzplätzen. Die Rückbank war ja schon seid Jahren entfernt und durch einen Einbau für Stauboxen ersetzt.
Leergewicht war auf der Wage 2220 kg Dabei waren etwas Werkzeug und zwei Sandbleche schon enthalten. In dem Zustand war der Wagen also über 300kg leichter als mit unserem Dachzelt!
Dazu, dass die Abnahme so reibungslos verlief, muss allerdings dazu sagen, ich hatte den TÜV schon über ein Jahr lang in die Umbaupläne eingebunden und vieles vorher durchgesprochen.
...Abrundungsradien aller Kannten (min 3mm), Außenabmessungen, erwartete Achsgewichte, Beleuchtung (Anordnung +Typ), Verwendung geprüfter Fenster, Der zweite Fluchtweg, Werkstoffe, Befestigung am Originalrahmen, usw.... War also nicht nach dem Motto “wir bauen mal was und - Hoppela hier bin ich: Trag mir das mal ein“
Nachdem diese Hürde also genommen war, konnte es daran gehen, den Wagen winterfertig zu machen. Wir hatten immerhin schon Oktober und auch wenn der Nachbarkater den neuen Schlafplatz dank fehlender Hecktür echt gut fand, so wollte ich den Wagen soweit geschossen bekommen um innen Heizen und weiterarbeiten zu können.
Als Hecktür habe ich eine Stauraumklappe aus dem „Tupperdosenzubehör“
genommen und den Ausschnitt für das Fenster ergänzt und mit Profilen etwas verstärkt. Durch das Klappdach müssen ja alle Fenster versenkt sein und dürfen nicht überstehen.
Als Verriegelung habe ich die original Verriegelungen der Heckklappe genutzt und mit einem Türschloss verbunden. Das dürfte auch über Jahre eine robuste und Wellblechpisten geeignete Variante sein.
Nun bekam die Kabine auch zwei Gasdruckdämpfer spendiert, die das Dach anheben und mit Fenstern und Tür ergab sich nun trotz niedriger Außentemperaturen die Möglichkeit über den Winter mit dem Innenausbau zu starten.
Davon mehr im dritten Teil zum Ausbau und den weiteren Arbeiten außen am Fahrzeug. Darunter auch die vordere Abstrebung, um die bei unseren Fahrzeugen leicht auftretenden Längsschwingungen zu unterdrücken, die auf Dauer nicht gut vom Rahmen vertragen werden.
Bei Fragen, Wünschen und Anregungen zum Bericht, einfach melden.
Mit besten Grüßen,
Bird
vielen Dank schon mal für das Feedback.
So eine lange Sylvesternacht und ein freier Tag ist gar nicht so verkehrt, daher schon heute und nicht erst wieder in einem Jahr der Teil 2 des Bauberichtes.

Da ich von Anfang an vorhatte, auf das Sandwich-Paneel eine (oder je nach Belastung mehrere) Lagen aus CFK und aus Gründen der höheren Schlagzähigkeit eine Decklage Aramid (Kevlar)/CFK Hybridgewebe aufzubringen, war ich nicht an den Einsatz von sonst üblichen Eckprofilen an den Stößen der Sandwichpaneele gebunden.
Damit war ich in der Formgebung der Kabine praktisch völlig frei und die Kabine hat wesentlich mehr Abschrägungen, als „Normale“ Kabinen bekommen.
Ja ja - 3D CAD Software verleitet immer zum spielen... Nur gut, dass der Entwurf nicht durch eine Arbeitsvorbereitung ging, die hätten mich wieder gelyncht

Ich wollt jedoch den Windwiderstand so gering wie möglich halten und die Kabine sollte auch nicht ganz so wuchtig auf dem kleinen Pickup wirken.... und ja zugegeben, man(n) möchte sich ja auch immer etwas von der Masse absetzen

Daraus ergab sich dann natürlich eine recht große Anzahl an Puzzleteilen die alle ohne Verschnitt passend gesägt werden mussten…
Für alle die ähnliches vorhaben, ich rate dazu für die Schnitte unbedingt eine Führungsschiene für Kreissägen zu besorgen. Ich hatte mir zwei mal 1,4m und noch eine 0,8m Schiene besorgt + die zugehörigen Verbinder. So konnte ich auch die längsten Schnitte mit über 3m in einem Stück sauber an der Schiene sägen.
Da ich alles nur in der kleinen Garage gemacht habe, hatte ich damit auch gleich das Problem gewonnen, wie die übereinander liegenden Paneele sägen, ohne das Untere gleich mit anzusägen...
Gelöst habe ich das Problem recht simpel mit 3cm starken Styroporplatten die ich jeweils immer über die komplette Fläche unter das oberste Paneel geschoben habe. So habe ich nur ca 5mm in das Styropor gesägt.
Was ich bei der Arbeit auch lieben gelernt habe ist eine Akku Kreissäge. Kein Kabelgezuppel, das sich garantiert irgendwo verhakt und ewig stört... Was unbedingt nicht sparen sollte ist eine gute und gute sitzende Staubmaske! Einige Schnitte habe ich gleich auch mit Absaugung durchgeführt, aber der Schlauch stört zugegeben doch auch wieder

Ohne Werbung machen zu wollen, aber von Makita gibt es seid ner Weile kleine 10,8V Maschinen. Unter anderem eine kleine Akku-Kreissäge und Akku-Stichsäge. Ein Traum für alle die Kleinteile und Öffnungen für Stauraumklappen. Die Arbeit soll ja auch Spaß bringen.
Wo wir gerade beim Thema Spaß sind... Auch wenn sich der ganze Umbau nun schon über einen ewigen Zeitraum hinstreckt, war der eigentliche Bau der Kabine dann doch eher Stress und weniger Spaß als erhofft.... Beruflich bedingt viel mehrfach der geplante Urlaub zum Bau aus, und die Zeit bis zum schon lange mit dem TÜV vereinbarten Termin für die Abnahme wurde eng... Letztendlich blieben dann genau 9 Tage um vom ersten Puzzle Teil ein vom TÜV abnahmefähiges Fahrzeug herzustellen

Also hieß es „Meter machen“ und gerade beim Laminieren ist so manch nicht so schöne Ecke dem Zeitdruck oder der Müdigkeit geschuldet... Die letzten Tage fingen Morgens gegen ca 8:30 an und endeten um 4 Uhr in der Früh... zusammen mit den Ausdünstungen von Harz und Aceton ist dann einem vieles egal

Aber zurück zum Bau. Nachdem die Puzzeleteile soweit ausgesägt waren habe ich den unteren Teil der Kabine über Kopf aufgebaut und erst einmal mit Tape zusammengefügt um noch eine letzte Pass-Kontrolle vorzunehmen und alles auszurichten. Ein paar große Zwingen ein Haufen kleinerer und Spanngurte sollten dabei unbedingt vorhanden sein.
Das von der Firma Paneeltec vorgeschlagene Körapop 225 ließ sich sehr gut verarbeiten und hatte eine hervorragende Klebeleistung. Vor allem ließ es sich auch mit dem passenden Lösungsmittel (noch nicht getrocknet) gut von der Oberfläche entfernen.
Ein Teil der Paneele wurden als Sitzfläche und Staubox gleich in die Kabine integriert. Dies führt gleichzeitig zu mehr Verwendungsstabilität bei gleichzeitig geringem Gewicht.
Die Längs und Querwände sind so angeordnet, das die Kräfte vom Fahrzeugrahmen optimal in die Kabine eingetragen werden und praktisch jede Wand vom Aufbau tragend ist, was die Kräfte gut verteilt.
Danach ging es an das erste Laminieren.
Die Firma „HP-Textiles“ konnte sich über diverse Aufträge freuen. Darunter:
- 65m² CFK/Aramid Hybridgewebe 205g/m2 Körper
- 25m² Kohlefasergewebe 420g/m2 Körper
- 20m² Kohlefasergewebe 245g/m² Körper
- 75m x 4cm Carbonband UniDirektional ca. 340g/m²
- Epoxi-System HP-E55L (Harz + Härter) Laminierharzsystem
- Epoxi-System HP-E40D (Harz + Härter) Deckschichtharzsystem
- Verdünner XB 5 Liter
- Abreissgewebe
- Viele Restbestände über "321...Meins"
Da die Liegefläche mit 210cm praktisch auf der Beifahrerseite über die komplette Länge „frei schwebt“ müssen hier die nur recht kurzen Wände die kompletten Biege-/ Zugkräfte aufnehmen. Auch der Boden muss dementsprechend stabil sein. Daher wurde hier erst mit 450g Gewebe gearbeitet und als Decklage das Hybridgewebe. In den Kanten wurde jeweils eine zweite Lage 450g/m² Gewebe verarbeitet um die Kräfte abzuleiten.
Die spätere Auflage für das Klappdach wurde in Form einer halbrund Holzleiste mit eingearbeitet.
Das Hybridgewebe mit Körperbindung ließ sich sehr gut drapieren und ließ sich somit auch sehr gut um die Kannten legen. Da sich das Hybridgewebe durch sein Kevlar kaum/praktisch nicht mit einer normalen Schere schneiden lässt, hatte ich mir neben einer Mikroverzahnten Schere einen „Easy Cutter“ Klick ich bin ein Link mit Mikroverzahnung gekauft. Auch wenn das gute Teil doch den Eindruck von viel „Plaste“ hinterlässt, doch absolut Top für diesen Einsatz!

Nachdem die Außenseite soweit fertig war, durfte der(die) Heizlüfter zeigen wofür unsere „grüner“ Strom so taugt und die Garage auf 40° zum Tempern für eine Nacht und einen halben Tag hochheizen.

Mehr war zeitlich leider nicht drin... Das Klappdach rief und so musste erst mal das Unterteil raus und gedreht werden. Obwohl eigentlich zu erwarten waren wir doch vom geringen Gewicht überrascht. Da ist das Dachzelt um Längen schwerer...

Problemlos ließ sich das Unterteil zu Zweit raustragen und auch drehen, ohne das es auseinanderbrach. So den ein oder anderen kritischen Blick der Nachbarschaft gab es dabei schon...
Nun wurde das ganze wieder „richtig herum“ in die Garage verfrachtet und der Deckel angepasst. Die große Herausforderung bestand nun darin, das durch den unteren offenen Querschnitt doch recht instabile Gebilde so auf Dauer zu bändigen, dass auch nach dem Zusammenbau der Spalt die gleiche Breite behält...sonst ist essig mit Abdichten...
Das war eigentlich auch meine größte Sorge beim Entschluss eine geteilte Kabine zu bauen und hat mich zwischenzeitlich zig mal wieder in die Richtung gezogen doch eine „Einteilige“ zu bauen. Letztendlich sorgt die spätere Dichtung auch noch für eine zusätzliche Spreizkraft .
Und als ob das ganze nicht schon schwer genug wäre, wollte ich den Deckel auch noch so stabil haben, dass ich auch noch drauf stehen kann oder etwas drauf verzurren kann. Das im geschlossenen Zustand nur ca. 4cm von der Seitenwand des Deckels über der des Unterteils stehen (rote Pfeile), macht die Sache nicht unbedingt einfacher... Also doch mal gut das man(n) Schiffbau studiert hat und aus Siebdruckplatte zwei Spanten (grüner Pfeil) ausgesägt und mit etwas Vorspannung eingeklebt und (bis das ganze laminiert ist) provisorisch verschraubt.
Kaum das der Kleber etwas Zeit hatte zu trocknen, kam der Deckel auch schon runter um in tiefer Nacht das Unterteil aus der Garage zu holen um die Hochzeit des Unterteils mit dem Untergestell zu starten. „Petrina“ (Ein Mann könnte beim Wetter noch so launisch sein) zeigte Einsicht und ließ am nächsten Tag die Sonne scheinen.

Um das Sandwich mit dem Metallgestell zu verkleben habe ich Sikaflex 260 verwendet. (Das im Gegensatz zum Körapop später wirklich überall seine Spuren hinterläst und man hat auch Wochenlang schöne schwarze Pfoten...) Über die Klebekraft lässt sich aber nicht meckern.
Tja nun ließ sich zum ersten Mal grob erkennen wie es später als Fahrzeug aussehen würde... Kurze Pause – Zum ersten Mal seid Tagen ein Teechen in Ruhe... Und weiter, Tag ist kurz...
Flugs das gute Wetter genutzt um den Liegebereich zu laminieren. (Ein Königreich für eine Halle)
Daher wurde hier wieder erst mit 450g Gewebe gearbeitet und in den Seitenwänden kam in Hauptbelastungsrichtung und als Kantenabschluss ein Unidirektionales Gelege zur Anwendung um die Zugkräfte aufzunehmen.
Schon jetzt konnte ich alleine durch die Außenlagen immerhin bis zur Vorderkannte robben um dort zu laminieren, ohne das die Liegefläche abbrach.
Sieg!

Auf dem Bild ist auch gut der Durchbruch zur Fahrerkabine zu sehen. Ich war schon erleichtert, als beide Ausschnitte tatsächlich deckungsgleich waren.
Schnell Abplanen und dann ging es die Nacht weiter daran den Deckel zu laminieren. Bis heute ärgert mich dabei eine Beule auf der Rückseite des Deckels, die man immer schön sieht von Hinten. Allerdings unter der Berücksichtigung, dass ich zu dem Zeitpunkt so gegen 03:30 bereits +18h Arbeit an dem Tag hinter mir und in den Knochen hatte wundert mich das es nur eine ist, die ich übersehen habe.

Den nächsten Tag durfte der Deckel auch bei ca 40° vor sich „hintempern“, während ich draußen den Übergang zwischen Unterteil und Metallgestell laminiert habe und die Auflageleiste, auf der der Deckel später im geschlossen Zustand liegen sollte. Schnell auch noch alle Übergänge geschliffen und die eine Stauraumklappe eingebaut. Der TÜV Termin rückte näher...
Am nächsten Tag dann der große Moment. Würde der Deckel auch nach dem Laminieren auf das Unterteil passen??? Zusammen mit unserem Nachbarn der sich netter Weise sofort zur Unterstützung angeboten hat, haben wir den Deckel aufgesetzt.
Und sitzt...in der Länge etwas knapp, aber passt!

Nun musste noch das Scharnier zum Klappen eingebaut werden. Dafür hatte ich mir überlegt einfach einen Bolzen zu verwenden. Woher Bolzen und Lager nehmen und nicht stehlen? Not macht erfinderisch, ich hatte noch von meinen alten Blattfedern die Bolzen aus den Federschäkeln und noch die Polyurethanlagerbuchsen. Also erst 8mm durchgebohrt und dann mit einer 32mm Lochsäge nachgebohrt. Lagerbuchsen mit angedicktem 5 min Epoxy eingesetzt und den Bolzen eingesetzt. Andere Seite ebenfalls und eine Stunde später der entscheidende Moment: Drehpunkt richtig gewählt, lässt sich der Deckel nun öffnen?
Er lies... Pühhhhh

Also schnell noch die Dachluke eingesetzt (Notwendig als zweiter Fluchtweg). Hatte mir dafür über „321..meins“ eine Bootsluke gekauft, die die geforderten 500x 500mm Innendurchmesser hat und neben abschließbar auch noch eine Stellung mit „Lüften“ hat, sprich sich mit nur wenigen mm Öffnung verriegeln lässt.
Am nächsten Morgen dann der Moment der Wahrheit: es ging zum TÜV. Die Hecktür war zwar noch nicht eingebaut und die Fenster lagen nur im Fahrzeug, aber... Details...

Ca. 1 ½ Stunden bangen und ich war stolzer Besitzer einer neuen Eintragung: „Teleskopierbarer Expeditionskoffer mit seitlichen Halterungen für Staukästen“ Doppelpühhhh alles soweit vom TÜV abgenommen.
Ich bin auf eigenen Wunsch weiterhin LKW geblieben (So hat mein Kleiner das Licht des Montagehalle erblickt und so soll er auch bleiben) allerdings nur noch mit zwei Sitzplätzen. Die Rückbank war ja schon seid Jahren entfernt und durch einen Einbau für Stauboxen ersetzt.
Leergewicht war auf der Wage 2220 kg Dabei waren etwas Werkzeug und zwei Sandbleche schon enthalten. In dem Zustand war der Wagen also über 300kg leichter als mit unserem Dachzelt!
Dazu, dass die Abnahme so reibungslos verlief, muss allerdings dazu sagen, ich hatte den TÜV schon über ein Jahr lang in die Umbaupläne eingebunden und vieles vorher durchgesprochen.
...Abrundungsradien aller Kannten (min 3mm), Außenabmessungen, erwartete Achsgewichte, Beleuchtung (Anordnung +Typ), Verwendung geprüfter Fenster, Der zweite Fluchtweg, Werkstoffe, Befestigung am Originalrahmen, usw.... War also nicht nach dem Motto “wir bauen mal was und - Hoppela hier bin ich: Trag mir das mal ein“
Nachdem diese Hürde also genommen war, konnte es daran gehen, den Wagen winterfertig zu machen. Wir hatten immerhin schon Oktober und auch wenn der Nachbarkater den neuen Schlafplatz dank fehlender Hecktür echt gut fand, so wollte ich den Wagen soweit geschossen bekommen um innen Heizen und weiterarbeiten zu können.
Als Hecktür habe ich eine Stauraumklappe aus dem „Tupperdosenzubehör“

Als Verriegelung habe ich die original Verriegelungen der Heckklappe genutzt und mit einem Türschloss verbunden. Das dürfte auch über Jahre eine robuste und Wellblechpisten geeignete Variante sein.
Nun bekam die Kabine auch zwei Gasdruckdämpfer spendiert, die das Dach anheben und mit Fenstern und Tür ergab sich nun trotz niedriger Außentemperaturen die Möglichkeit über den Winter mit dem Innenausbau zu starten.
Davon mehr im dritten Teil zum Ausbau und den weiteren Arbeiten außen am Fahrzeug. Darunter auch die vordere Abstrebung, um die bei unseren Fahrzeugen leicht auftretenden Längsschwingungen zu unterdrücken, die auf Dauer nicht gut vom Rahmen vertragen werden.
Bei Fragen, Wünschen und Anregungen zum Bericht, einfach melden.
Mit besten Grüßen,
Bird
Wir sind ein freies Land:
Hier kann jeder MEINE Meinung haben

Letzte Änderung: 01 Jan 2014 17:17 von Bird.
Folgende Benutzer bedankten sich: Ingo
Bitte Anmelden oder Registrieren um der Konversation beizutreten.
- Postman
-
- Offline
- Platinum Boarder
-
Weniger
Mehr
- Beiträge: 673
- Dank erhalten: 8
01 Jan 2014 17:44 #5
von Postman
L200 / Triton Magnum 03/2009
Postman antwortete auf Bird´s Baubericht - Expeditionskabine Ford Ranger
Tolle Arbeit , toller Bericht , meine Hochachtung

Gruß Peter / Postman


Gruß Peter / Postman
L200 / Triton Magnum 03/2009
Bitte Anmelden oder Registrieren um der Konversation beizutreten.
- boehsekuker
- Offline
- Junior Boarder
-
Weniger
Mehr
- Beiträge: 30
- Dank erhalten: 0
01 Jan 2014 21:09 #6
von boehsekuker

Schönes Ding...
boehsekuker antwortete auf Bird´s Baubericht - Expeditionskabine Ford Ranger



Schönes Ding...
Bitte Anmelden oder Registrieren um der Konversation beizutreten.
- Ingo
-
- Offline
- Administrator
-
02 Jan 2014 23:04 #7
von Ingo
...gesendet von meinem Desktop PC mit Röhrenmonitor....
Ingo antwortete auf Bird´s Baubericht - Expeditionskabine Ford Ranger
Hi, super ein Fortsetzungsroman!
Freue mich schon auf den nächsten Teil und die vielen schönen Bilder!
Gruß Ingo
Freue mich schon auf den nächsten Teil und die vielen schönen Bilder!
Gruß Ingo
...gesendet von meinem Desktop PC mit Röhrenmonitor....
Bitte Anmelden oder Registrieren um der Konversation beizutreten.
- Der Däne
-
- Offline
- Junior Boarder
-
Weniger
Mehr
- Beiträge: 21
- Dank erhalten: 3
09 Jan 2014 20:03 #8
von Der Däne
Offroader kommen in den Himmel.
Denn durch die Hölle sind wir schon gefahren.
Der Däne antwortete auf Bird´s Baubericht - Expeditionskabine Ford Ranger
Tolles Projekt, Bird 
Gruss,
Rolf

Gruss,
Rolf



Offroader kommen in den Himmel.
Denn durch die Hölle sind wir schon gefahren.
Bitte Anmelden oder Registrieren um der Konversation beizutreten.
- bb
-
- Offline
- Platinum Boarder
-
Weniger
Mehr
- Beiträge: 2321
- Dank erhalten: 494
09 Jan 2014 22:06 #9
von bb
bb antwortete auf Bird´s Baubericht - Expeditionskabine Ford Ranger
Tolles Projekt, ich bin absolut beeindruckt.
Das übertrifft imo die kommerziellen Anbieter von Individualausbauten um Längen, denn es ist genau auf die eigenen Bedürfnisse ausgerichtet. Ich bin gespannt, wie es weiter geht
Bernhard
Das übertrifft imo die kommerziellen Anbieter von Individualausbauten um Längen, denn es ist genau auf die eigenen Bedürfnisse ausgerichtet. Ich bin gespannt, wie es weiter geht

Bernhard
Bitte Anmelden oder Registrieren um der Konversation beizutreten.
- takanata
-
- Offline
- Platinum Boarder
-
Weniger
Mehr
- Beiträge: 1831
- Dank erhalten: 200
10 Jan 2014 09:15 #10
von takanata
Grüße aus dem Münsterland
Reinhard
takanata antwortete auf Bird´s Baubericht - Expeditionskabine Ford Ranger
Guten morgen Bird,
klasse, so eine bebilderte Darstellung eines Bauprojekts. So kann man sich das richtig vorstellen. Weiterso,
Bin gespannt auf die Fortsetzung.
klasse, so eine bebilderte Darstellung eines Bauprojekts. So kann man sich das richtig vorstellen. Weiterso,

Bin gespannt auf die Fortsetzung.
Grüße aus dem Münsterland
Reinhard
Bitte Anmelden oder Registrieren um der Konversation beizutreten.
Moderatoren: Elki, OffRoad-Ranger, Sisko, monty, BigPit
- Forum
- Drivers - Pub
- Markenunabhängige Themen
- Pickup Aufbauten, Wohnkabinen und Wohnwagen
- Bird´s Baubericht - Expeditionskabine Ford Ranger
Ladezeit der Seite: 0.103 Sekunden